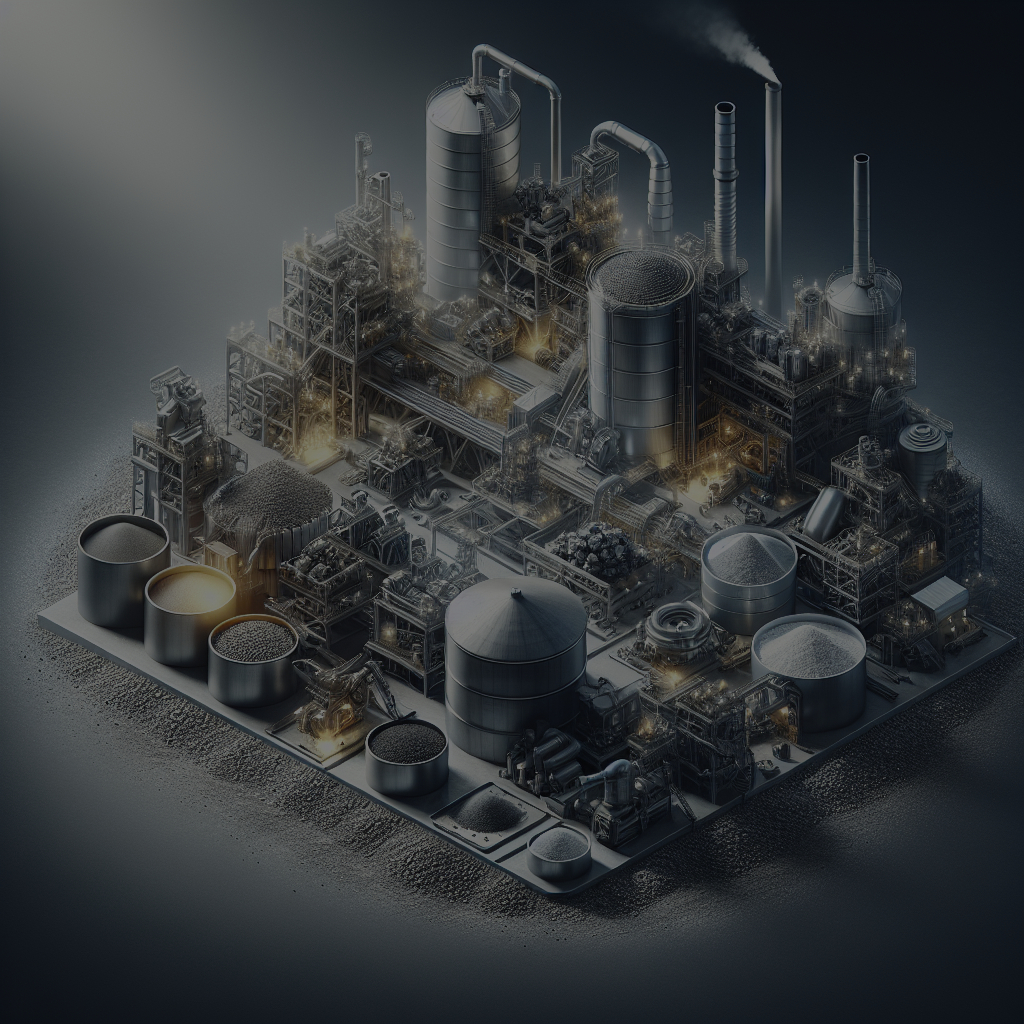
Przetwórstwo metali jest jednym z kluczowych sektorów przemysłu, który odgrywa istotną rolę w gospodarce globalnej. Proces ten obejmuje szereg etapów, począwszy od pozyskiwania surowców, poprzez ich obróbkę, aż po produkcję gotowych wyrobów. W niniejszym artykule przyjrzymy się podstawowym aspektom przetwórstwa metali, z uwzględnieniem technologii, metod oraz wyzwań, jakie napotykają przedsiębiorstwa działające w tej branży.
Pozyskiwanie i przygotowanie surowców
Proces przetwórstwa metali rozpoczyna się od pozyskiwania surowców, które są podstawą do dalszej obróbki. Surowce metaliczne mogą pochodzić z różnych źródeł, takich jak kopalnie, recykling czy import. W zależności od rodzaju metalu, proces wydobycia i przygotowania surowca może się znacznie różnić.
Wydobycie i transport
Wydobycie metali z ziemi jest pierwszym krokiem w łańcuchu przetwórstwa. Metale takie jak żelazo, miedź, aluminium czy złoto są wydobywane z kopalń odkrywkowych lub podziemnych. Proces ten wymaga zaawansowanej technologii oraz dużych nakładów finansowych. Po wydobyciu, surowce są transportowane do zakładów przetwórczych, gdzie poddawane są dalszej obróbce.
Przygotowanie surowców
Przygotowanie surowców obejmuje szereg procesów mających na celu oczyszczenie i przekształcenie surowego metalu w formę, która może być dalej przetwarzana. W zależności od rodzaju metalu, proces ten może obejmować kruszenie, mielenie, flotację, a także różne metody chemiczne i termiczne. Na przykład, w przypadku rudy żelaza, surowiec jest najpierw kruszony, a następnie poddawany procesowi wzbogacania, który polega na oddzieleniu żelaza od niepożądanych zanieczyszczeń.
Technologie i metody przetwórstwa metali
Po przygotowaniu surowców, następuje etap właściwego przetwórstwa, który obejmuje szereg technologii i metod mających na celu przekształcenie metalu w gotowy produkt. W zależności od rodzaju metalu oraz wymagań końcowego produktu, stosowane są różne techniki obróbki.
Obróbka plastyczna
Obróbka plastyczna jest jedną z najczęściej stosowanych metod przetwórstwa metali. Polega ona na kształtowaniu metalu poprzez jego odkształcanie pod wpływem sił mechanicznych. Do najważniejszych technik obróbki plastycznej należą:
- Kucie: Proces polegający na kształtowaniu metalu poprzez uderzenia młotem lub prasą. Kucie może być wykonywane na gorąco lub na zimno, w zależności od rodzaju metalu i wymagań końcowego produktu.
- Walowanie: Technika polegająca na przepuszczaniu metalu między walcami, co powoduje jego spłaszczenie i wydłużenie. Walowanie może być stosowane do produkcji blach, taśm, prętów i innych wyrobów.
- Tłoczenie: Proces polegający na kształtowaniu metalu poprzez jego wytłaczanie w matrycach. Tłoczenie jest często stosowane do produkcji elementów o skomplikowanych kształtach, takich jak części samochodowe czy obudowy urządzeń elektronicznych.
Obróbka skrawaniem
Obróbka skrawaniem to kolejna ważna metoda przetwórstwa metali, polegająca na usuwaniu nadmiaru materiału za pomocą narzędzi skrawających. Do najważniejszych technik obróbki skrawaniem należą:
- Toczenie: Proces polegający na obracaniu metalu wokół własnej osi i usuwaniu nadmiaru materiału za pomocą noża tokarskiego. Toczenie jest często stosowane do produkcji wałów, tulei i innych elementów o kształcie cylindrycznym.
- Frezowanie: Technika polegająca na usuwaniu materiału za pomocą obrotowego narzędzia skrawającego, zwanego frezem. Frezowanie jest stosowane do obróbki płaskich powierzchni, rowków, kształtów i innych elementów.
- Wiercenie: Proces polegający na wykonywaniu otworów w metalu za pomocą wiertła. Wiercenie jest powszechnie stosowane w produkcji elementów konstrukcyjnych, maszyn i urządzeń.
Obróbka cieplna
Obróbka cieplna to proces polegający na zmianie właściwości metalu poprzez jego nagrzewanie i chłodzenie. Do najważniejszych technik obróbki cieplnej należą:
- Hartowanie: Proces polegający na nagrzewaniu metalu do wysokiej temperatury, a następnie szybkim chłodzeniu w wodzie, oleju lub powietrzu. Hartowanie zwiększa twardość i wytrzymałość metalu.
- Odpuszczanie: Technika polegająca na nagrzewaniu zahartowanego metalu do umiarkowanej temperatury, a następnie powolnym chłodzeniu. Odpuszczanie zmniejsza kruchość metalu i poprawia jego plastyczność.
- Wyżarzanie: Proces polegający na nagrzewaniu metalu do określonej temperatury, a następnie powolnym chłodzeniu. Wyżarzanie poprawia strukturę metalu, zmniejsza jego twardość i zwiększa plastyczność.
Produkcja gotowych wyrobów
Po zakończeniu procesów obróbki, metal jest gotowy do produkcji gotowych wyrobów. W zależności od rodzaju produktu, proces ten może obejmować montaż, spawanie, malowanie, a także różne metody wykończeniowe.
Montowanie i spawanie
Montowanie i spawanie są kluczowymi etapami w produkcji gotowych wyrobów metalowych. Montowanie polega na łączeniu różnych elementów w jedną całość, natomiast spawanie to proces łączenia metali poprzez ich stopienie i zespolenie. Do najważniejszych technik spawania należą:
- Spawanie łukowe: Technika polegająca na łączeniu metali za pomocą łuku elektrycznego. Spawanie łukowe jest powszechnie stosowane w przemyśle budowlanym, motoryzacyjnym i stoczniowym.
- Spawanie gazowe: Proces polegający na łączeniu metali za pomocą płomienia gazowego. Spawanie gazowe jest często stosowane do naprawy i konserwacji elementów metalowych.
- Spawanie laserowe: Technika polegająca na łączeniu metali za pomocą wiązki laserowej. Spawanie laserowe jest stosowane w produkcji precyzyjnych elementów, takich jak części elektroniczne czy medyczne.
Wykończenie i kontrola jakości
Ostatnim etapem w produkcji gotowych wyrobów metalowych jest wykończenie i kontrola jakości. Wykończenie obejmuje różne procesy mające na celu poprawę wyglądu i właściwości powierzchni metalu, takie jak malowanie, galwanizacja, polerowanie czy anodowanie. Kontrola jakości polega na sprawdzeniu, czy gotowy produkt spełnia określone normy i wymagania. Proces ten może obejmować różne metody testowania, takie jak badania nieniszczące, pomiary wymiarowe czy testy wytrzymałościowe.
Wyzwania i przyszłość przetwórstwa metali
Przetwórstwo metali, mimo swojej długiej historii i zaawansowanych technologii, napotyka na szereg wyzwań, które mogą wpłynąć na przyszłość tej branży. Do najważniejszych wyzwań należą:
Ochrona środowiska
Przemysł metalurgiczny jest jednym z najbardziej energochłonnych i zanieczyszczających sektorów gospodarki. Wydobycie, przetwórstwo i produkcja metali generują znaczne ilości odpadów, emisji gazów cieplarnianych oraz zużywają duże ilości wody i energii. W związku z rosnącą świadomością ekologiczną oraz zaostrzającymi się regulacjami prawnymi, przedsiębiorstwa muszą inwestować w technologie i procesy mające na celu zmniejszenie negatywnego wpływu na środowisko.
Recykling i zrównoważony rozwój
Recykling metali jest kluczowym elementem zrównoważonego rozwoju przemysłu metalurgicznego. Proces ten pozwala na odzyskiwanie cennych surowców z odpadów, co przyczynia się do zmniejszenia zużycia surowców naturalnych oraz ograniczenia ilości odpadów. W przyszłości, rozwój technologii recyklingu oraz zwiększenie efektywności procesów odzyskiwania metali będą miały kluczowe znaczenie dla zrównoważonego rozwoju tej branży.
Innowacje technologiczne
Przemysł metalurgiczny, podobnie jak inne sektory gospodarki, musi stale inwestować w innowacje technologiczne, aby utrzymać konkurencyjność na rynku. Rozwój nowych materiałów, takich jak stopy o wysokiej wytrzymałości czy materiały kompozytowe, a także zaawansowane technologie obróbki, takie jak druk 3D czy obróbka laserowa, będą miały kluczowe znaczenie dla przyszłości przetwórstwa metali.
Podsumowując, przetwórstwo metali jest niezwykle ważnym i skomplikowanym procesem, który obejmuje szereg etapów, od pozyskiwania surowców, poprzez ich obróbkę, aż po produkcję gotowych wyrobów. W obliczu rosnących wyzwań związanych z ochroną środowiska, zrównoważonym rozwojem oraz innowacjami technologicznymi, przemysł metalurgiczny musi stale się rozwijać i dostosowywać do zmieniających się warunków rynkowych. Dzięki temu będzie mógł nadal odgrywać kluczową rolę w globalnej gospodarce, dostarczając niezbędnych materiałów i produktów dla różnych sektorów przemysłu.